Headstamp Guide - Letters - C
C
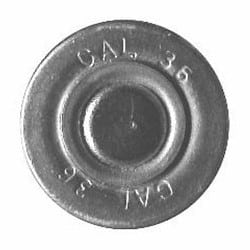
A Brief History
BRENNEKE OF AMERICA, L.P.
P.O. Box 1481
Clinton, Iowa 52733-1481
Tel.: (800) 753 9733
Fax: (563) 244 7421
E-mail: brennekeusa@clinton.net
URL: www.brennekeusa.com
BRENNEKE GMBH
Postfach 1646
D-30837 Langenhagen
Tel. +49 (0) 511-97262-0
Fax +49 (0) 511-97262-62
E-Mail: info@brenneke.de
URL: www.brenneke.de
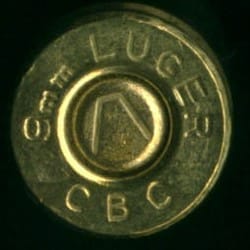
A Brief History
Magtech Ammunition Co., Inc.
6845 20th Avenue South Suite 120
Centerville, MN 55038
Toll Free: 1-800-466-7191
Tel: 651-762-8500
Fax: 651-429-9485
Magtech Website
Companhia Brasileira de Cartuchos
Av. Humberto de Campos 3220
09400 000 Ribeiaro Pires SP
Tel: +55 11 4822 8200
Fax: +55 11 4822 8323
CBC Website
From Website:
CBC Profile
CBC - Companhia Brasileira de Cartuchos is the largest military and commercial ammunition manufacturer in Latin America, and has over 60 years of small caliber military ammunition expertise. The high quality of CBC’s products is commercially recognized internationally under the brand name MAGTECH.
CBC Overview
CBC was founded in 1926 and from 1936 up to 1979, Remington Arms and ICI were the main shareholders. Today it is a totally privately owned Brazilian company and the principal share holder is the ARBI investment group.
CBC employs 1,200 people and produces more than 415 million rounds of ammunition each year. CBC’s manufacturing operations are ISO 9001 certified.
CBC’s main industrial complex is located in the city of Ribeirao Pires in the State of Sao Paulo, Brazil, in a vast green area of 500 acres with 377.000 square feet of built area. This key facility contains its ammunition, propellant powder and primer composition manufacturing operations, as well as its central offices. A second industrial complex, located in the south of Brazil is dedicated to the production of firearms and shot-shells.
All the ammunition lots produced at CBC are evaluated in the ballistic laboratory. Tests are monitored by very precise computers, which check for the ammunition performance, including velocity, pressure, accuracy and impact. All of these facilities are also available for the improvement and development of ammunition for all our customers. All ammunition is tested, from .22RF up to the 20 mm and 30 mm, used in military ships and aircrafts. All the information generated during the testing is automatically entered in the computer databases. Test facilities include six tunnels for ballistic tests, which range from 55 to 492 yards in length.
CBC offers a wide range of products for commercial and military use, including centerfire and rimfire ammunition of small and medium calibers, industrial cartridges, ammunition components, propellant powder, shotguns and rifles. CBC produces cartridges for both the civilian and military markets with calibers ranging from .22LR to 30 mm. As the arsenal for the Brazilian Armed Forces (Army, Navy and Air Force), besides supplying to several military forces worldwide, military ammunition has a daily average production of 1.000.000 rounds of 7.62 mm, 5.56 mm, .50 (12.7 x 99 mm), and other medium calibers and special rounds for training.
The maior volume production is the manufacturing of handgun ammunition for all calibers. The most popular cartridges produced today are calibers .380 AUTO, 40 S&W, 9 mm, 375MAG, 45AUTO, 44MAGNUM and .38. CBC also produces a wide range of rifle cartridges and shotshells. All commercial cartridges made by CBC are sold worldwide under the trade name “MAGTECH” and exported to more than 50 countries over two distribution centers, one in Minneapolis,MN, in the USA and the other in Hamburg, Germany. This ammunition is widely adopted by the Police in more than 20 countries and also by the Armed Forces worldwide.
About 80 percent of CBC’s firearms are exported and the export rate of the ammunition is approximately 70 percent of our total production. Products meet international regulations and are qualified by the Brazilian Armed Forces and the main proof houses in Europe.
The high quality of CBC’s products, recognized internationally, and the fact that it is currently exporting to over 50 countries, assures CBC a prominent position amongst the foremost manufacturers of ammunition and firearms in the world.
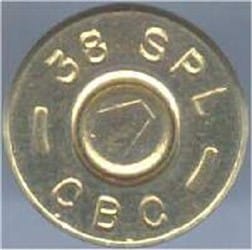
A Brief History
Magtech Ammunition Co., Inc.
6845 20th Avenue South Suite 120
Centerville, MN 55038
Toll Free: 1-800-466-7191
Tel: 651-762-8500
Fax: 651-429-9485
Magtech Website
Companhia Brasileira de Cartuchos
Av. Humberto de Campos 3220
09400 000 Ribeiaro Pires SP
Tel: +55 11 4822 8200
Fax: +55 11 4822 8323
CBC Website
From Website:
CBC Profile
CBC - Companhia Brasileira de Cartuchos is the largest military and commercial ammunition manufacturer in Latin America, and has over 60 years of small caliber military ammunition expertise. The high quality of CBC’s products is commercially recognized internationally under the brand name MAGTECH.
CBC Overview
CBC was founded in 1926 and from 1936 up to 1979, Remington Arms and ICI were the main shareholders. Today it is a totally privately owned Brazilian company and the principal share holder is the ARBI investment group.
CBC employs 1,200 people and produces more than 415 million rounds of ammunition each year. CBC’s manufacturing operations are ISO 9001 certified.
CBC’s main industrial complex is located in the city of Ribeirao Pires in the State of Sao Paulo, Brazil, in a vast green area of 500 acres with 377.000 square feet of built area. This key facility contains its ammunition, propellant powder and primer composition manufacturing operations, as well as its central offices. A second industrial complex, located in the south of Brazil is dedicated to the production of firearms and shot-shells.
All the ammunition lots produced at CBC are evaluated in the ballistic laboratory. Tests are monitored by very precise computers, which check for the ammunition performance, including velocity, pressure, accuracy and impact. All of these facilities are also available for the improvement and development of ammunition for all our customers. All ammunition is tested, from .22RF up to the 20 mm and 30 mm, used in military ships and aircrafts. All the information generated during the testing is automatically entered in the computer databases. Test facilities include six tunnels for ballistic tests, which range from 55 to 492 yards in length.
CBC offers a wide range of products for commercial and military use, including centerfire and rimfire ammunition of small and medium calibers, industrial cartridges, ammunition components, propellant powder, shotguns and rifles. CBC produces cartridges for both the civilian and military markets with calibers ranging from .22LR to 30 mm. As the arsenal for the Brazilian Armed Forces (Army, Navy and Air Force), besides supplying to several military forces worldwide, military ammunition has a daily average production of 1.000.000 rounds of 7.62 mm, 5.56 mm, .50 (12.7 x 99 mm), and other medium calibers and special rounds for training.
The maior volume production is the manufacturing of handgun ammunition for all calibers. The most popular cartridges produced today are calibers .380 AUTO, 40 S&W, 9 mm, 375MAG, 45AUTO, 44MAGNUM and .38. CBC also produces a wide range of rifle cartridges and shotshells. All commercial cartridges made by CBC are sold worldwide under the trade name “MAGTECH” and exported to more than 50 countries over two distribution centers, one in Minneapolis,MN, in the USA and the other in Hamburg, Germany. This ammunition is widely adopted by the Police in more than 20 countries and also by the Armed Forces worldwide.
About 80 percent of CBC’s firearms are exported and the export rate of the ammunition is approximately 70 percent of our total production. Products meet international regulations and are qualified by the Brazilian Armed Forces and the main proof houses in Europe.
The high quality of CBC’s products, recognized internationally, and the fact that it is currently exporting to over 50 countries, assures CBC a prominent position amongst the foremost manufacturers of ammunition and firearms in the world.
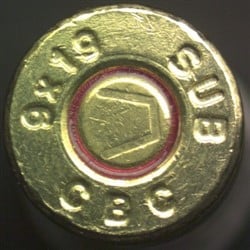
A Brief History
Headstamp of "CBC SUB" seen on ammunition from Magtech Subsonic ammunition. See CBC headstamp for more information on the company.
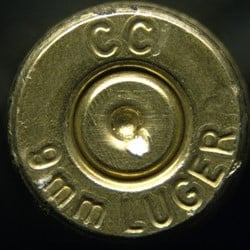
A Brief History
From website: "Capital Cartridge has been supplying once-fired brass shell casings for commercial and recreational reloading since 2012." Their website features quantities of washed and polished fired cartridge cases of various headstamps both with and without the fired primers. The only cartridge cases with the headstamp of "CC" are sold new and unprimed on their website. Assembled Capital Cartridge handgun ammunition with CC headstamps are sold on their sister company's website (2A Warehouse). They feature both rifle and handgun calibers.
Other products listed on their website include primers and bullets.
Contact information:
9702 Wallisville Rd, Suite B Houston, TX 77013
832-831-2684
info@capitalcartridge.com
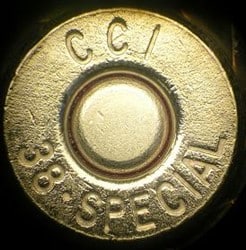
A Brief History
2299 Snake River Ave.
Lewiston, ID 83501
Phone: (208)-799-3944
Fax: (208)-798-3397
From Website:
A History of CCI®
Richard ”Dick” Speer (1915-1994) possessed a remarkable talent for things mechanical. He was a machinist at Boeing Aircraft's Seattle plant when his realized that his brother Vernon's success in the component bullet business meant there was money to be made in reloading.
The brothers found another niche that they felt held opportunity. There were a number of proprietary rifle cartridge like the Weatherby and Newton designs that were not supported by the ”big” ammo companies. Dick decided to make cases to service this small but active market. He left Seattle and joined Vernon in Lewiston, Idaho. In a small room at the Speer bullet plant, he began production of these special cases using an impact extrusion process.
Speer's cases were first sold under the name, "Forged from Solid", before changing it to Speer Cartridge Works. Later, market confusion over to companies with ”Speer” in the name led Dick and his partner Arvid Nelson to change the name to Cascade Cartridges, Inc., or CCI.
Although Dick's case-making process was sound, the quality of the raw material was not. In the early post-war years, most stocks of cartridge brass had been depleted for the war effort. Faced with an untenable situation, Dick turned to a different path.
Component primers for reloaders were in short supply. Some war surplus primers were showing up but the supply and choice was limited. Dick decided to get into the component primer business. He found a refugee scientist from Lithuania, Dr. Victor Jasaitis, and brought him to Lewiston in 1951. Dr. Jasaitis, or "Doc" to most people, was a specialist in explosive chemistry, and developed the exotic chemicals and processes needed for primer manufacture. Although Dick intended to build primers for hobby reloaders, his first shipment was to fulfill an military contract, using the chlorate FA-70 formula. Then he turned to non-corrosive, non-mercuric formulas for sporting cartridges, and reloaders now had a steady supply of rifle and pistol primers that was unheard of previously.
To handle the new business, Dick Speer bought a 17-acre chicken "ranch" next to the Lewiston Gun Club just a mile south of brother Vernon's bullet works. The farmhouse doubled as an office and warehouse, and production began in a renovated chicken coop. He quickly erected modern labs and manufacturing buikdings, gaining him room to expand the product line. When the gun club moved, Dick bought the adjoining property for future expansion. The CCI plant still occupies that property today.
In 1957, Dick added shotshells to the line and, two years later, began making industrial powerloads for powder-actuated fastener systems. In 1962, he expanded into rimfire ammunition with Mini-Mag, still our most popular rimfire product.
In 1967, an Oregon firm, Omark Industries, was seeking an in-house source of loads for the powder-actuated tools they manufactured, and bought CCI from Dick Speer. Seeing the profitability of sporting ammo and components, they wisely elected to let CCI continue to grow in this area. New products such as Stinger, the world's first hypervelocity 22 Long Rifle ammo, rolled out of the CCI facility.
In 1980, CCI entered the centerfire ammunition market with Blazer®. This innovative products used aluminum cartridge cases and high-tech manufacturing processes to create effective, low-cost ammunition for training and practice.
In 1986, CCI's development engineers set out on a comprehensive primer improvement program to meet the requirements of progressive loading equipment that was starting to dominate the reloading market. The program wrapped up in 1989 with the introduction of all-new primers that featured smooth feeding through automated equipment, reduced residue in non-magnum primers, improved primer seating, and better sensitivity that included a larger "sweet spot" for firearms that produced off-center firing pin strikes.
In 1991, CCI opened a new, state-of-the-art primer manufacturing facility to insure that we could supply all our customers' needs. During the so-called "primer shortage" of 1993-94, CCI was the only US primer manufacture to continuously ship primers to commercial accounts, largely due to the increased capacity afforded by this new facility. CCI is also a major supplier of military cannon primers.
In 1990, CCI perfected the first hypervelocity 22 Magnum Rimfire cartridge, and has continued to add new rimfire products like Mini-Mag™ Silhouette, Quik-Shok, and Velocitor™, the fastest 40 grain 22 Long Rifle load on the market.
A Brief History Of CCI® Blazer® Centerfire Ammunition
Including some Frequently Asked Questions
In the late 1970's, US ammunition makers were faced with increasing costs and competition from cheap imports. At CCI-Speer, our premium Lawman® ammunition with high-performance bullets appealed to serious sport shooters and peace officers, but was more than the casual shooter needed. We set out to find a way to offer these shooters economical ammunition that could be priced lower than many imports yet provide American-made quality. As the 38 Special was the most popular handgun cartridge then, the project was known internally as "Low-cost 38's."
We knew that the cartridge case was the single most expensive component of a modern cartridge. Significant costs savings in the other components were not realistic, so we investigated ways that would take costs out of the case without compromising safety or function. The areas of raw material, production processes, labor, and scrap rates all had to be considered.
Raw material costs vary through the year with supply and demand, but we could take cost out of a case by investigating materials other than cartridge brass. We looked at other grades of brass, several classes of polymer plastics, steel, various grades of aluminum, and other materials. Of these, the best candidate was an aircraft-grade aluminum that could be heat-treated for strength. Although cartridge brass and this grade of aluminum cost about the same per pound, one pound of aluminum yields more cases than one pound of brass. We had a material-now the question was, "Can we build cases at a decent internal cost?"
To do this, it meant having a good process and controlling scrap rates. We found the equipment needed to form and heat-treat aluminum cases. We sourced a raw material format that reduced scrap rates from the 30 percent of conventional case forming to a tiny two percent. Over the period of a year, scrap rate improvement alone would yield impressive savings.
We entered this project targeting the 75 percent of the shooting market that does not reload, so several aspects of an aluminum case that affected reloadability played well with a cartridge for the non-reloader. To discourage reloading of Blazer cases, and to gain a small savings on primer cost, we elected to go with efficient Berdan priming. In the Berdan system, the anvil moves from the primer to the case. Adding a Berdan anvil to a case is free; in a Boxer primer it is a separate part with its own cost.
Original Blazer cases used an odd primer diameter (0.195 inch) to further discourage reloading. This was eventually changed when we started loading higher pressure cartridges like the 9mm Luger and 357 Magnum. They needed the extra material in the case head that a 0.175 inch primer pocket affords. From that point on, we used a standard .175 inch Berdan pocket in all cartridges that took a small pistol primer.
An early problem came up. Although cases were heat-treated "by the book," they were not springing away from revolver chamber walls as they should. We discovered the problem was "the book," not the material. All published aluminum heat treat references were prepared with large part like landing gear struts in mind. The techniques did not translate to small parts. Out of necessity, CCI rewrote the book on aluminum heat treatment. We made numerous breakthroughs in this field that gave us a strong case and a leadership position in this technology.
The final case was ready for market. The savings were partially due to getting more cases per pound of raw material, but the savings in processing and the all-important scrap rate were as significant. The economical case was a multi-discipline success that grew directly out of smart engineering.
The cases were done, and a new, more efficient loading line was built to reduce direct labor costs and increase throughput. The later had a remarkable positive effect on the bottom line. We went "outside the box" to develop a loading system that was not previously used for centerfire ammunition. It was safe, efficient, and enabled us to change caliber set-ups easily to quickly react to incoming orders. In 1981, the first Blazer ammunition was introduced to the market. It was 38 Special, loaded with a 158 grain round nose lead bullet. Blazer was on it way.
Today, Blazer is a highly evolved product. Through constant testing and improvement, we have overcome the objections that traditional shooters found to a non-brass cartridge case. The number of Blazer calibers increased to 13 today. We offer a selection of bullet weights and types not found in most imports or "white box" domestic ammo.
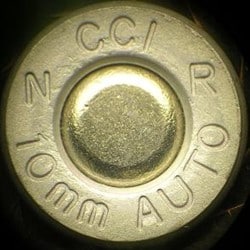
A Brief History
2299 Snake River Ave.
Lewiston, ID 83501
Phone: (208)-799-3944
Fax: (208)-798-3397
From Website:
A History of CCI®
Richard ”Dick” Speer (1915-1994) possessed a remarkable talent for things mechanical. He was a machinist at Boeing Aircraft's Seattle plant when his realized that his brother Vernon's success in the component bullet business meant there was money to be made in reloading.
The brothers found another niche that they felt held opportunity. There were a number of proprietary rifle cartridge like the Weatherby and Newton designs that were not supported by the ”big” ammo companies. Dick decided to make cases to service this small but active market. He left Seattle and joined Vernon in Lewiston, Idaho. In a small room at the Speer bullet plant, he began production of these special cases using an impact extrusion process.
Speer's cases were first sold under the name, "Forged from Solid", before changing it to Speer Cartridge Works. Later, market confusion over to companies with ”Speer” in the name led Dick and his partner Arvid Nelson to change the name to Cascade Cartridges, Inc., or CCI.
Although Dick's case-making process was sound, the quality of the raw material was not. In the early post-war years, most stocks of cartridge brass had been depleted for the war effort. Faced with an untenable situation, Dick turned to a different path.
Component primers for reloaders were in short supply. Some war surplus primers were showing up but the supply and choice was limited. Dick decided to get into the component primer business. He found a refugee scientist from Lithuania, Dr. Victor Jasaitis, and brought him to Lewiston in 1951. Dr. Jasaitis, or "Doc" to most people, was a specialist in explosive chemistry, and developed the exotic chemicals and processes needed for primer manufacture. Although Dick intended to build primers for hobby reloaders, his first shipment was to fulfill an military contract, using the chlorate FA-70 formula. Then he turned to non-corrosive, non-mercuric formulas for sporting cartridges, and reloaders now had a steady supply of rifle and pistol primers that was unheard of previously.
To handle the new business, Dick Speer bought a 17-acre chicken "ranch" next to the Lewiston Gun Club just a mile south of brother Vernon's bullet works. The farmhouse doubled as an office and warehouse, and production began in a renovated chicken coop. He quickly erected modern labs and manufacturing buikdings, gaining him room to expand the product line. When the gun club moved, Dick bought the adjoining property for future expansion. The CCI plant still occupies that property today.
In 1957, Dick added shotshells to the line and, two years later, began making industrial powerloads for powder-actuated fastener systems. In 1962, he expanded into rimfire ammunition with Mini-Mag, still our most popular rimfire product.
In 1967, an Oregon firm, Omark Industries, was seeking an in-house source of loads for the powder-actuated tools they manufactured, and bought CCI from Dick Speer. Seeing the profitability of sporting ammo and components, they wisely elected to let CCI continue to grow in this area. New products such as Stinger, the world's first hypervelocity 22 Long Rifle ammo, rolled out of the CCI facility.
In 1980, CCI entered the centerfire ammunition market with Blazer®. This innovative products used aluminum cartridge cases and high-tech manufacturing processes to create effective, low-cost ammunition for training and practice.
In 1986, CCI's development engineers set out on a comprehensive primer improvement program to meet the requirements of progressive loading equipment that was starting to dominate the reloading market. The program wrapped up in 1989 with the introduction of all-new primers that featured smooth feeding through automated equipment, reduced residue in non-magnum primers, improved primer seating, and better sensitivity that included a larger "sweet spot" for firearms that produced off-center firing pin strikes.
In 1991, CCI opened a new, state-of-the-art primer manufacturing facility to insure that we could supply all our customers' needs. During the so-called "primer shortage" of 1993-94, CCI was the only US primer manufacture to continuously ship primers to commercial accounts, largely due to the increased capacity afforded by this new facility. CCI is also a major supplier of military cannon primers.
In 1990, CCI perfected the first hypervelocity 22 Magnum Rimfire cartridge, and has continued to add new rimfire products like Mini-Mag™ Silhouette, Quik-Shok, and Velocitor™, the fastest 40 grain 22 Long Rifle load on the market.
A Brief History Of CCI® Blazer® Centerfire Ammunition
Including some Frequently Asked Questions
In the late 1970's, US ammunition makers were faced with increasing costs and competition from cheap imports. At CCI-Speer, our premium Lawman® ammunition with high-performance bullets appealed to serious sport shooters and peace officers, but was more than the casual shooter needed. We set out to find a way to offer these shooters economical ammunition that could be priced lower than many imports yet provide American-made quality. As the 38 Special was the most popular handgun cartridge then, the project was known internally as "Low-cost 38's."
We knew that the cartridge case was the single most expensive component of a modern cartridge. Significant costs savings in the other components were not realistic, so we investigated ways that would take costs out of the case without compromising safety or function. The areas of raw material, production processes, labor, and scrap rates all had to be considered.
Raw material costs vary through the year with supply and demand, but we could take cost out of a case by investigating materials other than cartridge brass. We looked at other grades of brass, several classes of polymer plastics, steel, various grades of aluminum, and other materials. Of these, the best candidate was an aircraft-grade aluminum that could be heat-treated for strength. Although cartridge brass and this grade of aluminum cost about the same per pound, one pound of aluminum yields more cases than one pound of brass. We had a material-now the question was, "Can we build cases at a decent internal cost?"
To do this, it meant having a good process and controlling scrap rates. We found the equipment needed to form and heat-treat aluminum cases. We sourced a raw material format that reduced scrap rates from the 30 percent of conventional case forming to a tiny two percent. Over the period of a year, scrap rate improvement alone would yield impressive savings.
We entered this project targeting the 75 percent of the shooting market that does not reload, so several aspects of an aluminum case that affected reloadability played well with a cartridge for the non-reloader. To discourage reloading of Blazer cases, and to gain a small savings on primer cost, we elected to go with efficient Berdan priming. In the Berdan system, the anvil moves from the primer to the case. Adding a Berdan anvil to a case is free; in a Boxer primer it is a separate part with its own cost.
Original Blazer cases used an odd primer diameter (0.195 inch) to further discourage reloading. This was eventually changed when we started loading higher pressure cartridges like the 9mm Luger and 357 Magnum. They needed the extra material in the case head that a 0.175 inch primer pocket affords. From that point on, we used a standard .175 inch Berdan pocket in all cartridges that took a small pistol primer.
An early problem came up. Although cases were heat-treated "by the book," they were not springing away from revolver chamber walls as they should. We discovered the problem was "the book," not the material. All published aluminum heat treat references were prepared with large part like landing gear struts in mind. The techniques did not translate to small parts. Out of necessity, CCI rewrote the book on aluminum heat treatment. We made numerous breakthroughs in this field that gave us a strong case and a leadership position in this technology.
The final case was ready for market. The savings were partially due to getting more cases per pound of raw material, but the savings in processing and the all-important scrap rate were as significant. The economical case was a multi-discipline success that grew directly out of smart engineering.
The cases were done, and a new, more efficient loading line was built to reduce direct labor costs and increase throughput. The later had a remarkable positive effect on the bottom line. We went "outside the box" to develop a loading system that was not previously used for centerfire ammunition. It was safe, efficient, and enabled us to change caliber set-ups easily to quickly react to incoming orders. In 1981, the first Blazer ammunition was introduced to the market. It was 38 Special, loaded with a 158 grain round nose lead bullet. Blazer was on it way.
Today, Blazer is a highly evolved product. Through constant testing and improvement, we have overcome the objections that traditional shooters found to a non-brass cartridge case. The number of Blazer calibers increased to 13 today. We offer a selection of bullet weights and types not found in most imports or "white box" domestic ammo.
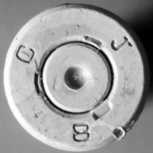
A Brief History
NORINCO
12A Guang An Men Nan Jie,Beijing,China
P.O.Box 2932 Beijing
Post Code: 100053
Telephone: (8610)63529988
Facsimile: (8610)63540398
E-mail: info@norinco.com.cn
NORINCO Website
From Website:
China North Industries Corporation (NORINCO) is an enterprise group engaged in both products and capital operation, integrated with R&D, manufacturing, marketing, and services. NORINCO mainly deals with defense products, international engineering contracting, optronic products, chemical products, sports arms & equipment, automobiles and logistics services, etc.
NORINCO faces toward the markets and strives for development of updated high-tech defense products. NORINCO has demonstrated the solid strength of Chinese national defense industry and technology in precision strike systems, amphibious assault weapons and equipment, long-range suppression weapon systems, anti-aircraft & anti-missile systems, information & night vision products, high-effect destruction systems, anti-terrorism & anti-riot products as well as small arms. NORINCO has won trust from clients for its high quality products and excellent services.
While having built its brands in such services as international engineering contracting, logistics and automobiles, NORINCO maintains its competitive edge in chemicals, optronic products, and sports arms based on the integration of technology, manufacturing and trade. NORINCO's subsidiary has been registered in the lead of the global 225 largest international engineering contractors for successive years, and many NORINCO's subsidiaries have also been awarded the national title as advanced enterprise for excellent quality and performance.
By advocating collaboration and mutual benefit, and having made constant efforts to enhance the capabilities of taking the whole situation into account on management of its overseas and domestic markets, NORINCO has established a global operation and information network and formed a worldwide-diversified market setup.
NORINCO will continue to promote product innovations, improve technology & service, share the achievements of development and build a better future with our domestic and international friends!
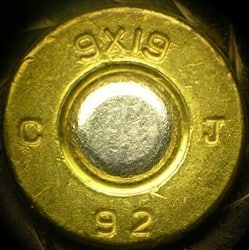
A Brief History
Norinco
12A Guang An Men Nan Jie,Beijing,China
P.O.Box 2932 Beijing
Post Code: 100053
Telephone: (8610)63529988
Facsimile: (8610)63540398
E-mail: info@norinco.com.cn
NORINCO Website
From Website:
China North Industries Corporation (NORINCO) is an enterprise group engaged in both products and capital operation, integrated with R&D, manufacturing, marketing, and services. NORINCO mainly deals with defense products, international engineering contracting, optronic products, chemical products, sports arms & equipment, automobiles and logistics services, etc.
NORINCO faces toward the markets and strives for development of updated high-tech defense products. NORINCO has demonstrated the solid strength of Chinese national defense industry and technology in precision strike systems, amphibious assault weapons and equipment, long-range suppression weapon systems, anti-aircraft & anti-missile systems, information & night vision products, high-effect destruction systems, anti-terrorism & anti-riot products as well as small arms. NORINCO has won trust from clients for its high quality products and excellent services.
While having built its brands in such services as international engineering contracting, logistics and automobiles, NORINCO maintains its competitive edge in chemicals, optronic products, and sports arms based on the integration of technology, manufacturing and trade. NORINCO's subsidiary has been registered in the lead of the global 225 largest international engineering contractors for successive years, and many NORINCO's subsidiaries have also been awarded the national title as advanced enterprise for excellent quality and performance.
By advocating collaboration and mutual benefit, and having made constant efforts to enhance the capabilities of taking the whole situation into account on management of its overseas and domestic markets, NORINCO has established a global operation and information network and formed a worldwide-diversified market setup.
NORINCO will continue to promote product innovations, improve technology & service, share the achievements of development and build a better future with our domestic and international friends!
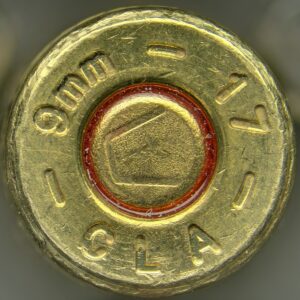
A Brief History
Caracal Light Ammunition (CLA), a Tawazun Holding subsidiary, produces a range of diversified calibers and ammunition types for both the military and sport sectors.
Established in 1994, CLA began as a facility with the capacity to produce three to five million rounds per year. CLA prides itself on supplying clients with quality, dependable ammunitions, which comply with the highest international standards.
Today, CLA operates large, exclusive ammunition production lines in its Abu Dhabi plant.
In this medium-sized facility, the company develops military-grade ammunition, from 5.56mmx45mm ammunition to 9mmx19mm, for clients such as the UAE Armed Forces, police departments and shooting clubs.
In addition to its military use products, the commercial ammunition CLA produces for hunting and competition shooting is also gaining a growing reputation for its excellent quality in the global market.
Caracal Light Ammunitions (CLA) - Army Technology
PO Box 76243,
Abu Dhabi,
United Arab Emirates
This ammunition was also found in a LAHAB branded box.
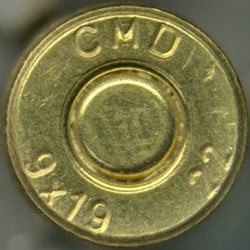
A Brief History
This ammunition is manufactured by Piney Mountain Ammunition Company out of Texas, who makes 22 Long Rifle, 9mm Luger, and 45 Auto caliber tracer cartridges. According to their website,they appear to only do wholesale business at this time. This particular headstamp was found on a Stormfire Tracer Ammunition product being sold on Dragon Black Armory's website.
Contact information:
https://www.pineymountainammunitionco.com/index.html
3101 N Highway 183
Liberty Hill, TX 78642
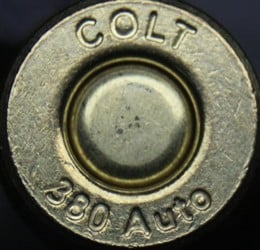
A Brief History
In 2016, Colt partnered with Double Tap to produce 2 lines of ammunition: Colt National Match and Colt Defense.
https://www.guns.com/news/2016/06/09/doubletap-teams-with-colt-for-new-ammo-line
An additional line of cartridges loaded with solid copper hollow point (SCHP) bullets has been produced but at this time (1/2020), it is unclear who is making them.
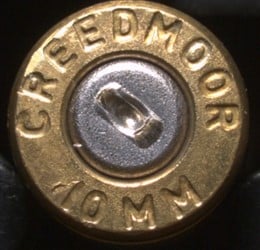
A Brief History
Creedmoor Ammunition, sold by Creedmoor Sports, Inc. From their website, this is Starline brass with their headstamp on it. Sold in calibers 6.5 Creedmoor, 223 Rem, 45 Auto, 10mm, 38 Special, and 40 S&W.
Contact:
custserv@creedmoorsports.com
https://www.creedmoorsports.com/search?search_keyword=creedmoor&x=12&y=8
167 Creedmoor Way
Anniston, AL 36205
1-800-273-3366